Rubber to Plastic Conversions for Cost and Weight Savings
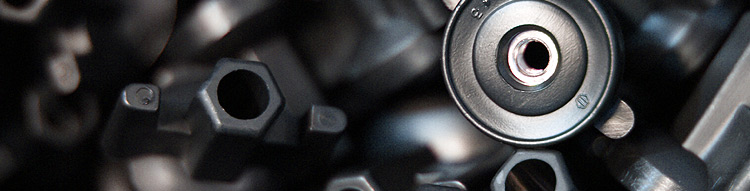
Recent dramatic increases in the cost of natural rubber has driven interest in alternative materials that can react and perform like vulcanized rubber. Many products requiring rubber-like, elastomeric properties are found in demanding environments. Often, extended exposure to high temperatures and certain chemical fluids can begin to dry-out vulcanized rubber, changing its physical properties to less than original application requirements. If elastomeric properties are required for the application, they are generally needed across a wide temperature range. Vulcanized rubber has a tendency to have wide variations in hardness from extreme hot to extreme cold temperatures. This usually changes the elastomeric performance originally intended for the application.
The engineers of Engineered Plastics Company (EPC), a division of MacLean-Fogg Component Solutions have had great success in helping our customers resolve many of these issues by converting to a thermoplastic elastomer that can be processed on standard injection molding machines. Thermoplastic elastomers act and perform very similar to many vulcanized rubber materials but with some distinct advantages.
The Hood Leveler product we have developed provides a piece price cost reduction and a product performance enhancement as the thermoplastic elastomer demonstrates smaller hardness variation over a wider temperature range. This has helped our customer to achieve no hood damage on low temperature extreme hood slam testing. The old Rubber component often becomes very hard at lower temperatures and loses some of its important energy absorbing properties.
The Hood Isolation Bumper also results in a piece price reduction but more importantly, offers regulatory design advantages that the old rubber extruded cut-off profile simply could not meet.
EPC engineers use geometric stiffing to achieve an acceptable performance level instead of just thicker, heavier walls of rubber, thereby also offering a weight reduction. The design also pleases Styling teams due to the new rounder, smoother look now available thru injection molding. Internal regulatory requirements of having part numbers, company logo, and material reprocessing codes visible on the part all came along at no cost as these elements were now able to be molded into the part at desired locations. Read more about these products by clicking here.
EPC engineering has decades of experience in materials, tooling, processing and plastics product design utilizing the latest software tools for precise evaluation. Let us help you on your next project with ‘out-of-the-box’ thinking, powerful capabilities and extensive experience to insure your success.
Related Products
Have comments or feedback to this paper, please feel free to contact us by clicking here.